Key takeaway:
- The location of a warehouse is crucial in warehouse construction as it impacts warehouse efficiency and profitability in eCommerce businesses.
- Proper planning and selection criteria should be considered when constructing a warehouse to ensure it is tailor-made, efficient, and fit for its intended purpose.
- Factors such as structural building loads, utility of space, preliminary stages, noise levels, cost, time savings, labor costs, existing building design, and outdoor storage should be carefully evaluated during the warehouse construction process.
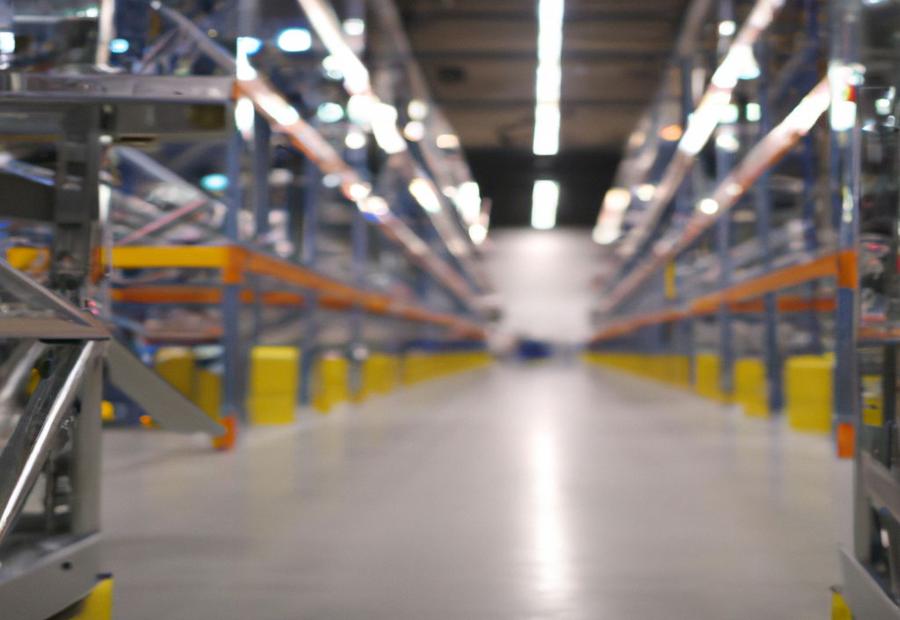
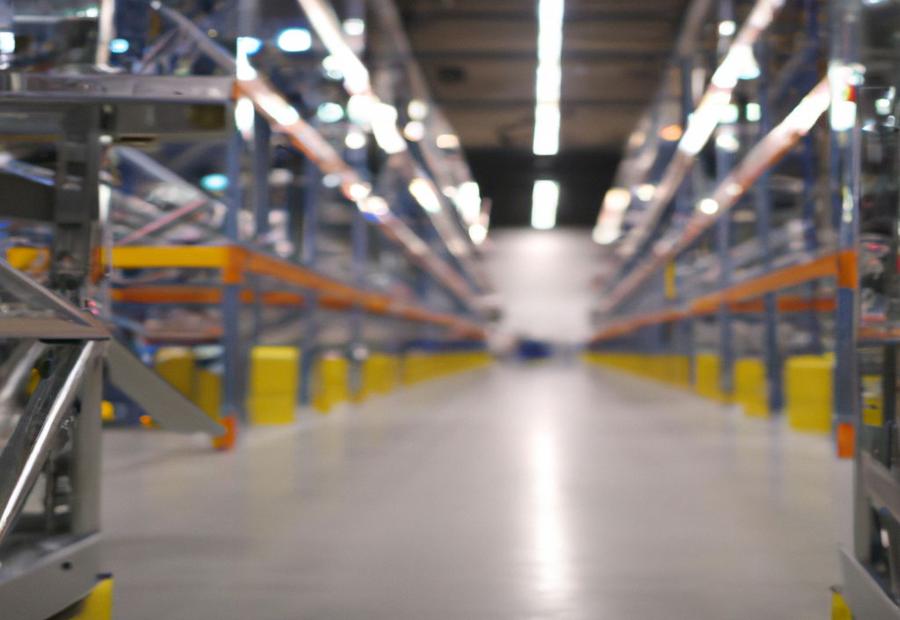
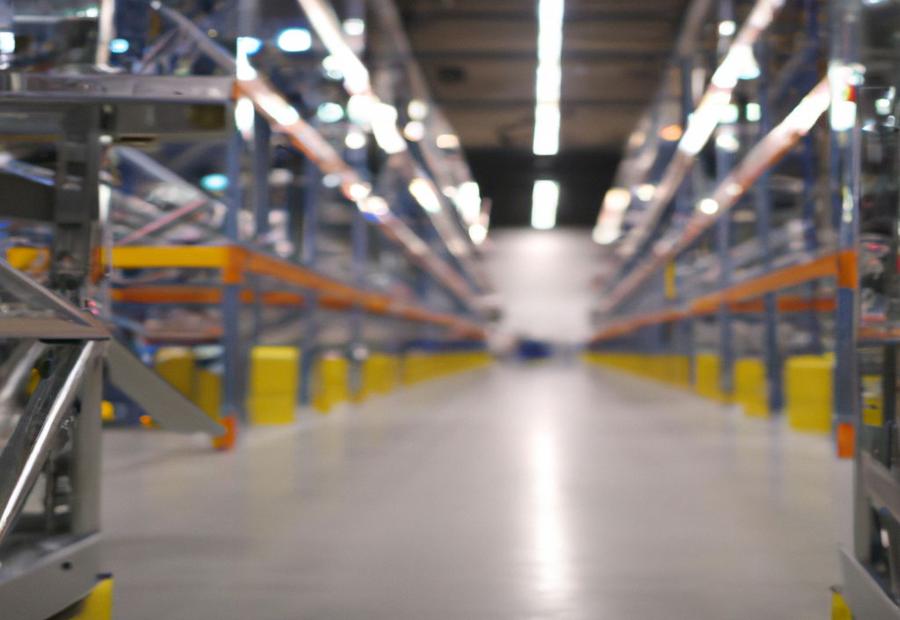
Photo Credits: Build-Wire.Com by Michael Garcia
Selecting the right location is crucial in warehouse construction, as it directly impacts efficiency and profitability for eCommerce businesses. Finding an optimal site ensures smooth operations, reduces transportation costs, and minimizes delivery time. For instance, according to the Reference Data, warehouses located near major transportation hubs witness higher productivity rates and increased customer satisfaction. The subsequent sub-sections will explore the significance of location in warehouse construction and delve into its direct influence on warehouse efficiency and eCommerce business profitability, providing valuable insights for decision-makers in the industry.
Importance of Location in Warehouse Construction
The value of a good location for warehouse construction cannot be overestimated. Placement of warehouses is vital for the success and efficiency of eCommerce businesses. A good location can significantly boost profitability by optimizing supply chain management and ensuring timely distribution to customers.
When planning warehouse construction, several things must be taken into account. It’s essential to have an appropriate plan and selection criteria to find the best location. Building loads and use of space should also be thoughtfully considered, as they affect warehouse efficiency. Bespoke solutions that are fit for purpose will ensure maximum productivity and cost-effectiveness.
As well as these factors, noise levels during construction and the planning stage leading up to final design are critical to creating an optimal warehouse location. Cost and time savings, including minimizing labor costs, are important in assessing a site’s feasibility.
Also, existing building designs can impact warehouse construction. Retrofitting may be needed to meet specific requirements. Cost savings and speed of construction can be achieved with efficiently manufactured precast concrete panels.
Moreover, an experienced design and construct team is necessary to ensure all aspects of the warehouse’s location are considered. Proximity to target audiences should also be taken into account when selecting a site, as it can lead to increased customer satisfaction and loyalty.
Moreover, tightly-controlled processes and access to raw materials are essential for efficient warehouse operations. By optimizing these factors, warehouses can achieve cost savings that benefit the end user.
Furthermore, warehouse layout considerations such as storage systems and equipment must be carefully planned to maximize efficiency during operations.
In conclusion, careful consideration of each aspect is indispensable for selecting an optimal location for warehouse construction. By thoroughly weighing these key factors throughout the decision-making process, businesses can position themselves for success in today’s competitive eCommerce landscape.
Impact on Warehouse Efficiency and eCommerce Business Profitability
Constructing a warehouse that is efficient and profitable for eCommerce businesses requires proper planning and selection criteria. These include the layout, design, and accessibility of the facility. Strategically placed storage areas, loading docks, and delivery zones streamline operations. Building loads, structural utility, and noise level assessment are also essential. Optimize space with features like mezzanine floors or automated conveyor systems. Customize the facility to fit its purpose. Consider product size, inventory turnover rates, and storage conditions. Experienced design and construct teams are important for optimizing storage space and implementing lean processes. Constructing a successful warehouse is like writing a suspenseful novel – it’s all about location, structure, and a killer team.
Key Factors to Consider in Warehouse Construction
Photo Credits: Build-Wire.Com by Jerry Jackson
When it comes to warehouse construction, there are several key factors that must be carefully considered. From proper planning and selection criteria to the utility of space and structural building loads, it’s crucial to create a tailor-made solution that is both efficient and fit for purpose. The preliminary stages, planning, and final design all play a role in ensuring cost and time savings, while the expertise of an experienced design and construct team helps deliver the desired outcome. The warehouse layout, structural components, and skilled workforce further contribute to the overall success of the project.
Proper Plan and Selection Criteria
A well-crafted plan is a must for warehouse construction! It helps to make best use of space and resources, leading to improved efficiency. Selecting the right location is also essential for success. These factors are crucial for the profitability of an eCommerce business.
- Plan ahead: At the start, plan the layout, size, purpose, and future expansion possibilities.
- Cost & Time Savings: Optimal utilization of space, streamlined processes, and minimal labor costs can save you money and time.
- Evaluate existing buildings: Assess the suitability of an existing building design for the warehouse to modify and enhance its features to meet requirements.
- Utilize precast concrete panels: These panels are manufactured off-site, reducing labor time while preserving structural integrity.
Moreover, consider noise levels, design & construct teams, outdoor storage options, raw materials, cost optimization, warehouse layout, and skilled workforce to achieve desired outcomes.
To guarantee success and profitability for your eCommerce business, it is important to incorporate proper planning and selection criteria. Optimize space, cut costs, evaluate existing building designs, and utilize precast concrete panels to create a warehouse that meets your needs while staying within budget and timeframe. Make the right decisions and get optimal results!
Structural Building Loads and Utility of Space
Structural building loads and utility of space are major factors for efficient operations and maximizing profit. Planning and selection criteria must be optimal to use space and accommodate loads. Tailor-made solutions are essential to enhance warehouse functionality. Noise levels, design & cost savings all factor in maximizing utility & efficiency.
Efficiently produced precast concrete panels provide robust support and time & cost savings. Experienced design & construct teams are crucial for managing structural building loads. Consider customer base & machine operators to determine layout and other components. A skilled workforce handles tasks for effective functioning.
Pro Tip: Maximize storage capacity while minimizing floor space usage by implementing racking systems that optimize vertical space utilization.
Tailor Made Solution and Fit for Purpose Outcome
A tailor-made solution for warehouse construction means customizing and optimizing the design and layout to fit specific needs. This guarantees a fit-for-purpose outcome. To get there, factors like space usage, workflow optimization, and required equipment must be taken into account.
Maximizing storage, streamlining operations, and boosting productivity are possible by making the design and layout match the business or industry’s needs. Cost and time savings can be achieved with efficient manufacturing techniques and precast concrete panels.
A professional design and construct team is key to a successful outcome. They have expertise in optimizing warehouse layouts and selecting appropriate materials. Plus, efficient machine operators are a must for smooth operations. Training programs should be set up to develop their skills.
In conclusion, a tailor-made solution brings many advantages: optimized space utilization, enhanced operational efficiency, cost savings, and a workforce equipped with the necessary skills for optimal performance. Building a warehouse is like conducting a symphony – it calls for careful planning and a conductor to block out the noise.
Preliminary Stages and Noise Levels
Decision-making and planning for warehouse construction must begin early. Factors like location, layout, and space use must be considered. Also, noise levels should be kept in mind to create a good work atmosphere.
Selection and Planning: Selecting the right spot for the warehouse is essential. Proximity to transportation, target audience, and cost must all be taken into account.
Structural loads and space: Evaluate structural loads for the intended use. Optimize the space for maximum storage capability.
Tailor-made solutions: Design the warehouse based on specific needs. Think of material moving machines, operators, and fit-for-purpose outcome.
Cost and time savings: Planning can save money and time. Consider labour costs, design teams, processes, and raw materials.
Existing building design: Evaluate existing buildings for reuse or renovation. This may result in cost savings while meeting project requirements.
Prioritize these aspects during the preliminary stages. Focus on noise level management and proper planning for a successful warehouse construction project.
From planning to perfection: Building a flawless warehouse design with no room for mistakes.
Planning Stage and Final Design
Planning and design are essential for warehouse construction projects. Think about planning criteria, structural loads, space utilization, tailor-made solutions, material handling equipment operators’ needs, and desired customer bases. This can save costs and create productive warehouses. Don’t miss this stage – get help from experienced design teams who know how to create efficient outcomes!
Cost and Time Savings and Labour Costs
Cost and time savings are key when considering labor costs in warehouse construction. By managing resources well, expenses can be cut and productivity optimized. Factors like selecting the right location, proper planning, and tailor-made solutions all play a role in reducing labor costs and improving efficiency. Experienced design and construct teams, processes that are tightly controlled, and skilled workforces are also helpful.
A Table with “Factor” and “Impact” columns could provide an overall view of cost and time savings related to labor costs in warehouse construction. For example, factors such as experienced design and construct teams, or tightly controlled processes could make a big difference in terms of labor costs.
It’s important to look into unique details that might help to save on cost and time in warehouse construction. This could include the target customer base and the skills of material moving machine operators. By understanding the requirements of the target audience and having skilled operators, operations can be optimized while labor costs are minimized. Additionally, using efficient manufacturing methods like precast concrete panels can speed up construction timelines and reduce expenses.
To save on cost and time in warehouse construction projects, these tips could be followed:
- Research potential locations thoroughly to find areas with reasonable price rates and close to the target audience.
- Invest in modern technology and equipment to drive efficiency and reduce manual labor needs.
Finally, lean management principles can streamline processes, cut waste, and ultimately save on overall costs.
By following these tips and looking into the various factors mentioned above, companies can make big savings in terms of cost and time, while managing their labor costs effectively in warehouse construction projects.
Existing Building Design and Warehouse Construction Project
The design of an existing building is vital for a warehouse construction project. It’s the basis for the entire project and decides how effective the warehouse will be. Pay attention to the structure, layout, and function for optimal storage and operation.
Consider factors like the strength of the building and use of space. Make sure the design is suited for your needs, such as storage, inventory systems, and any unique features.
Think about any disruption that could occur during construction, i.e. noise. Plan well for the design stage to save time and money. Take into account accessibility, safety regulations, workflow, and equipment.
Utilize manufacturing methods to speed up construction, such as precast concrete. An experienced design and construct team will guarantee the existing building design is managed properly.
Using the right approach for an existing building design will result in a functional warehouse. This will ensure a successful transition from construction to operation without affecting daily business activities.
Efficiently Manufactured and Precast Concrete Panels
Efficiently manufactured and precast concrete panels have become a favorite in warehouse construction. These panels are designed using advanced production techniques to guarantee they meet the required standards for strength, durability, and performance.
One of the benefits of these panels is that they can be produced off-site in a controlled environment. This leads to faster construction times and fewer on-site labor requirements. Thus, these panels offer substantial savings in time and money during the building process.
Also, precast concrete panels offer outstanding structural integrity and load-bearing capacity. They are designed to carry heavy loads, making them great for warehouse operations. With high precision and efficiency of manufacturing, these panels provide a sturdy and reliable solution for warehouses of all sizes.
Moreover, these panels are highly customizable. They can be tailored to the particular needs of each warehouse project. Adjusting dimensions, incorporating specialized features, and integrating insulation – efficiently manufactured and precast concrete panels can be customized to deliver an ideal outcome.
In summary, the use of these panels in warehouse construction has many advantages. From quicker construction times to reinforced structural integrity, these panels are a great choice for any warehouse project.
Major Undertaking and Outdoor Storage
Incorporating outdoor storage into a warehouse construction project is a huge task. It comes with its own set of issues. One challenge is to use the space outside effectively while still keeping it efficient and reachable. Warehouse managers must think about storage layouts, aisle widths, and material handling equipment.
Another issue is the environmental factors that can harm the stored items. For instance, temperature changes and moisture. To prevent this, design solutions must be included in the warehouse construction. This can include drainage systems to stop water and structures to protect against weather. Plus, security measures must be taken to protect valuable inventory.
Outdoor storage is necessary for many industries such as manufacturing, retailing, and logistics. When planning out the outdoor storage, warehouse managers must think about their needs and requirements. This includes inventory volume, product characteristics, accessibility needs, and security considerations. By doing this, businesses can ensure efficient operations and maximize profits.
Experienced Design and Construct Team
Experienced designers and construction professionals are key for warehouse construction. Their knowledge and expertise ensure the design and construction process is efficient. This leads to a well-built and functional warehouse. Reference data underlines the importance of having an experienced design and construct team at the start of the project.
They decide structural building loads, utility of space, and overall design. The team also makes sure the warehouse is suited for its purpose. Noise levels, cost savings, labor costs, and outdoor storage requirements are all considered. Reference data highlights the need for an experienced team to collaborate in the planning stage and finalize the design.
Having an experienced design and construct team brings cost and time savings. They can use precast concrete panels for efficient manufacturing. This speeds up construction and uses high-quality materials. Additionally, their experience lets them manage existing building designs or site conditions while making necessary modifications for warehouse construction.
Desired Customer Base and Material Moving Machine Operators
Warehouse construction requires both a desired customer base and skilled material moving machine operators. This helps operations run smoothly and is key to meeting customer demands. Designing a warehouse that considers both groups involves creating strategic layouts, optimizing workflow, and ensuring accessibility. It also needs suitable equipment and machinery. Knowing their needs allows for tailored warehouses and improved efficiency.
Safety and ergonomics should also be considered when building a warehouse. This includes safety measures, lighting, ventilation, and ergonomic workstations. This boosts employee satisfaction, reduces accidents, and increases productivity.
Research suggests that having a desired customer base impacts profitability. Thus, when constructing a warehouse, the target audience’s preferences and needs should be taken into account.
In conclusion, considering the requirements of customers and machine operators when constructing a warehouse will optimize it for efficiency, safety, and employee satisfaction. This ultimately enhances operational productivity.
Tightly Controlled Processes and Raw Materials
Efficient warehouse construction needs processes that are strictly controlled and raw materials that have certain standards. This monitoring guarantees quality and productivity. By having strict control, mistakes, waste, and productivity can all be reduced.
To get tightly controlled processes and good quality raw materials, certain key factors must be included in the construction project. A reliable supplier for consistent quality materials must be chosen. This will give warehouses raw materials that fit their requirements and reach industry standards. Standard operating procedures and quality control systems must be put into place, too.
More details about the factors contributing to tightly controlled processes and the use of raw materials can be seen in a table. Inspections and audits are necessary to find any possible problems or non-compliance with regulations. Guidelines must be established for handling and storing raw materials, and safety protocols must always be followed. Training programs for staff members can teach them the best practices for monitoring and maintaining quality control.
A Pro Tip: A real-time monitoring system with sensors and automation technology can help with control over processes and early detection of any issues with raw material handling. This proactive approach can make cost savings by taking care of problems before they become bigger.
Cost Savings and End User
The cost savings in warehouse construction are a crucial factor that affects the end user. Various components contribute to these cost savings. They include the proper planning and selection criteria, efficient precast concrete panels manufacturing, and tight control of raw materials. The end-user profits from such cost savings, with reduced expenses and increased profitability for the eCommerce business.
The table below summarises the key cost-saving factors and their effects on the end user:
Key Factors | Impact on End User |
---|---|
Proper planning and selection criteria | Reduced expenses |
Efficient manufacturing of precast concrete panels | Profitability boost |
Tightly controlled processes in terms of raw materials | Improved efficiency |
It’s also essential to consider other factors, like the desired customer base. By understanding the target audience and offering an affordable rate, the end user can attract more customers while keeping profitability. This means that when making decisions about a warehouse location, both the cost savings and the needs of the end user must be considered.
Building the right foundation: Planning the layout and structural components for optimal warehouse efficiency and comedic potential.
Warehouse Layout and Other Structural Components
Warehouse construction has an important aspect. It’s the layout and structure of the facility. Design and organization of the space are key parts of reaching efficiency and max productivity. This involves racks, aisles, workstations and structural elements like columns, beams, roof trusses, walls and flooring.
Warehouse Layout | Structural Components |
Arrangement of racks, aisles, workstations to use the space. | Elements that give stability and durability. |
Organizing helps workflow, inventory and navigation. | Columns, beams, trusses, walls, flooring. |
Other details must be taken care of during warehouse construction. Fire safety, security systems, ventilation, insulation. This will keep employees safe, and goods from damage or theft.
Improve efficiency even more with:
- Automation systems for better processes.
- Flexible shelving or pallet racking that can be adjusted.
- RFID (Radio Frequency Identification) to track inventory.
- Energy-efficient lighting to cut costs and maintain illumination.
These will boost productivity, reduce errors and lessen costs.
A strong and efficient warehouse is like an amazing team, and you need a talented workforce to make it run like clockwork.
Skilled Workforce
Skilled employees are a must for successful warehouse construction. Their expertise and knowledge are key for efficient and effective operations. They help manage inventory, fulfill orders, and keep the workflow smooth. Experienced staff can boost productivity, reduce errors and downtime, and enhance operational performance.
To ensure skilled workers, recruitment strategies, training programs, and employee development initiatives must be considered. The selection process should target individuals with experience and expertise in warehousing. Regular training should be offered to keep them up-to-date with advances and best practices, thus improving their skills and flexibility.
Moreover, a positive work environment that encourages teamwork, collaboration, and learning is critical for developing a skilled workforce. Furthermore, offering competitive packages and growth opportunities can attract more motivated candidates.
Warehouse Location Decisions
Photo Credits: Build-Wire.Com by Noah Robinson
Making strategic decisions regarding warehouse location is paramount when it comes to warehouse construction. In this section, we will explore factors such as target audience, reasonable price rates, and suitable places for warehouse location. By analyzing these crucial elements, we can optimize warehouse efficiency, customer accessibility, and ultimately enhance business success.
Target Audience and Reasonable Price Rate
Incorporating the target audience and reasonable price rate into warehouse location decisions is essential. Assessing customers’ needs and pricing strategies helps businesses find the right location. A comprehensive table can be made, with customer demographics, cost analysis, pricing strategies and market trends. This allows businesses to identify their target audience and set a reasonable price rate that meets their expectations.
When constructing a warehouse, unique details related to the target audience and pricing need to be taken into account. Consider customer preferences, market competition, and economic trends. This will ensure the chosen location and price rate are right for the intended audience. Examining these details can increase profitability and success in eCommerce.
Finding the best warehouse location is like playing hide and seek, with your bank account as the seeker!
Suitable Places for Warehouse Location
For a warehouse to be suitable, many things must be taken into account. Consider the target audience and the cost. It should be accessible for customers and have an affordable rate. Close proximity to transportation networks such as highways and ports should be taken into account for efficient shipment of goods.
Points to Consider:
- Transportation Networks: Ensure easy access to highways, railways, and ports. This will make the delivery of goods quick and cheap.
- Skilled Workforce: Find a location with skilled material moving machine operators who can handle goods adeptly.
- Suitable Infrastructure: Utilities such as power and water supply should be present. There should be sufficient space for parking and the maneuvering of vehicles.
- Local Regulations: Check the local regulations and permitting processes to avoid any legal complications.
Unique Details:
These factors will help pick a warehouse that is efficient and delivers to customers on time. Through a thorough assessment of target audience, transportation networks, skilled workforce, infrastructure, and local regulations, businesses can make a smart choice regarding their warehouse location.
Conclusion
Photo Credits: Build-Wire.Com by Arthur King
Constructing a warehouse involves several key points to consider. Location is one important factor; it must be strategically placed for efficient distribution of goods. Size and layout of the warehouse are also crucial. Design should allow for storage and retrieval of goods with maximum efficiency. Materials used should be durable and able to cope with the demands of a warehouse environment. Advanced technologies and automation systems can increase productivity and streamline operations. Taking all factors into account is essential for successful construction of a warehouse. This is key for optimizing logistics and success of the business.
Some Facts About Key Factors to Consider in Warehouse Construction:
- ✅ The design, layout, infrastructure, and systems are all key factors in warehouse efficiency. (Source: Team Research)
- ✅ Precast concrete panels are a valuable option in warehouse construction, offering structural strength and time and cost savings. (Source: Team Research)
- ✅ Combining precast panels with structural steel as a construction system can further enhance time and cost efficiencies in warehouse construction. (Source: Team Research)
- ✅ Choosing the right location for a warehouse is crucial for the success of an eCommerce business, considering factors such as layout, workforce availability, transportation linkages, and regulations. (Source: Team Research)
- ✅ Warehouse location should also consider the size of the facility and its ability to accommodate inventory and future expansion. (Source: Team Research)
FAQs about Key Factors To Consider In Warehouse Construction
What are the key factors to consider in warehouse construction?
When constructing a new warehouse, there are several key factors to consider:
- Warehouse layout and design: The design of the warehouse should maximize space utility and consider the type of operations to be conducted inside it.
- Availability of skilled workforce: Choosing a location with an adequate supply of skilled labor is crucial for smooth operations.
- Business requirements: The warehouse should be designed to meet the specific needs and requirements of the business, such as storage capacity and material handling capabilities.
- Shipping preparation: Considerations should be given to the location’s proximity to major linkages and transportation modes to facilitate efficient shipping and logistics.
- Operation efficiencies: Factors such as the use of precast concrete panels and structural steel can contribute to time and cost savings in the construction process.
- Regulations and compliance: It is important to understand and adhere to relevant regulations and policies when choosing a warehouse location.